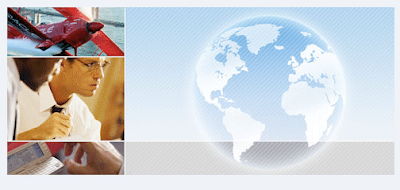
To make use of the minimum and maximum stock level settings defined for a subinventory within Oracle Inventory you can make use of the Min-max planning report. To start this report, or schedule it you have to go to you concurrent requests screen and start a new single request. The name of the concurrent request is "Min-max planning report". There are numerous parameters which can be set for this concurrent request.
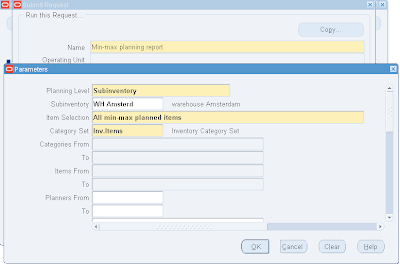
planning level states if you want to run the report on organization level which will include all the subinventories of the organization or on a specific subinventory. If you pick the last you will have to define the subinventory.
Item selection:
Here you can state the selection of the items you want to include in the report. You can pick all the items that have a current stock level below the minimum stock level, include only the items which have currently more stock than the max stock level or include all items.
Category set:
You have to set a category set, by default it will be set for inventory item however a other item category for the items to be included on the min-max planning report can be chosen.
Item Category:
Item category families and categories can be set to even more finely grain the selection of items you can set to be included in the final report.
Items from (to):
A range of items can be set if you want a defined set of items. You can use this option to run the report only for a single item. In this case you define the same item number in the from and to field.
Planners:
The same as can be done for items in the item from and item to fields can be done for the planners. You can run the report for a specific planner of group of planners.
Buyers:
the same as can be done for items and planners can be done for buyers. You can run the report for a specific buyer or set of buyers. This can be very useful when you (as a buyer) want to run the report for the items you are responsible for.
Sort By:
Sort by will influence the order of the items on the report. It can be set to Item, Category, Buyer or Planner.
Demand cutoff date:
The report includes demand on or before this date. If you do not check Net Demand this calculation is for display purposes only. You can also set the offset for this date.
Supply cutoff date:
The calculation for the includes open supply orders on or before this date.
Restock:
Here you can state if you want to do a restock automatically based upon the outcome of the report. When you set it to yes the system will create requisitions. If you run the report on organization level it will also run make jobs for the items where you have stated it is a make item.
For Repetitive Items:
"If you are using the Organization Planning Level, choose one of the following For Repetitive Item options: Create Requisitions for items under minimum quantity, Create Discrete Jobs for items under minimum quantity or run the Report Only without creating jobs or requisitions"
Default Delivery To:
Default Delivery To enables you to set a default deliver to location. This is only used when you use the restock = yes option.
Net Unreserved Orders, Reserved Orders, WIP Demand:
If set to yes the reserved, unreserved orders and the WIP demand will be subtracted from the total available stock on the given date so you will get a good indication what the stock will be on this given date and what the demand for restock will be on this date.
Include PO Supply, Move Order Supply, WIP supply, Interface:
If set to yes the calculation will take in account the quantity which will be delivered for this date based upon purchase orders, move orders, WIP jobs and non-nettable subinventories.
Lot Control:
here you will be able to state if items which are under lot control should be included in the report.
Display Format:
Here you will be able to set the way the report is displayed and what it will contain.
Display Item Description:
Include the item description in the report or not.
No comments:
Post a Comment